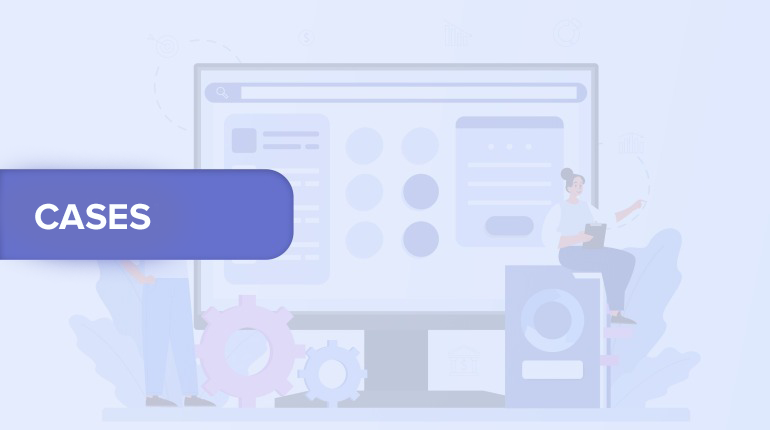
Lean Smart Transformation of RIR-Quadra
Client
Joint Stock Company "Rosatom Infrastructure Solutions" (RIR) is a division of the State Corporation "Rosatom" and one of the largest energy companies in Russia. The company ensures stable energy supply to consumers across 16 regions, supplies electricity to the wholesale market, and manages heat and water supply networks spanning over 5,000 km. RIR holds approximately 25% of the district heating market in the Central Federal District.
Additionally, RIR provides heat, steam, and electricity to key enterprises of Rosatom, including the Siberian Chemical Combine, Chepetsk Mechanical Plant, and Ural Electrochemical Plant. RIR combines expertise in energy, utilities, resource supply, and digital solutions for urban environments, positioning itself as a reliable partner in regional development.
Project Overview
In 2022, the energy company PAO "Quadra" became part of RIR. To integrate this new asset into Rosatom, a transformation approach called "Lean Smart Transformation" was developed:
Lean – restructuring business processes
Smart – creating a digital model of a unified company and automating processes
Transformation – managing change, working with people, and integrating into the Rosatom ecosystem
Project Duration: March 2022 – December 2023
Project Goal
The primary objective was to integrate the new assets while maintaining operational stability during the transformation.
Project Background
A key challenge was a highly compressed timeline—integrating a legal entity with over 12,000 employees into Rosatom’s management structure within two years, ensuring uninterrupted operational and administrative processes.
A hypothesis was formed that such a challenge could be addressed through a synergy of project and process approaches, combining process visualization, alignment of key operations, and a high level of communication and change management support.
Resources Involved
A Project Office was established, consisting of nine experts in business analysis and IT development, along with a business trainer, HR, and PR specialists to ensure effective change management.
Project Implementation
The Lean Smart Transformation approach enabled the company and employees to prepare for the merger, implement new processes, and transition to a process-oriented management model.
Business process mapping helped unify operations across both companies, clearly defining responsibilities, including during functional mergers and personnel optimization.
A quick start and automation of routine tasks demonstrated the efficiency of the approach, reducing resistance to new processes.
The creation of a "Change Team" allowed for bottom-up project initiatives, supporting grassroots innovation.
Comprehensive communication support accompanied each transformation step, including multichannel updates, employee training, and feedback mechanisms. This ensured employee engagement, onboarding into Rosatom’s corporate culture, and seamless adaptation to new ways of working.
The process model represents a digital process twin, developed in the SILA Union software.
Figure 1. Business architecture of the unified company, consisting of elements connected at a systemic level.
A total of 44 top-level processes and more than 300 second-level processes have been identified.
Figure 2. Top-level processes.
Figure 3. Example of second-level processes.
To map third-level processes, a team of methodologists was formed and trained, including representatives from each business function. Their responsibilities, in addition to modeling, included ensuring the alignment of the mapped processes with related methodologists and managers, which allowed for the establishment of horizontal communication necessary for integrating two different legal entities.
Figure 4. Example of third-level processes.
Figure 5. Example of the company’s documentation diagram.
In parallel with building business processes, the change management team initiated and implemented 30 projects aimed at improving operational efficiency, achieving a total economic effect exceeding 100 million rubles. Some of these projects were selected for further automation.
Utilized Functionality of SILA Union Software
SILA Union is used as a process repository, document storage, and organizational structure representation tool. Importantly, all objects are interconnected at the system level. The ability to process data using scripts enabled effective task execution related to process workload assessment and optimization, as well as the generation of various reports according to the requirements of different Rosatom departments for IT strategy development, business architecture description, and more.
Figure 6. IT Systems Registry
Project Stages
The project consisted of three parallel tracks:
Creation of the process model
Process optimization
General timeline for organizational changes
For process modeling, a classic top-down approach was adopted, starting with the identification of top-level processes, describing and linking second-level processes, and providing a detailed description of third-level processes in BPMN notation.
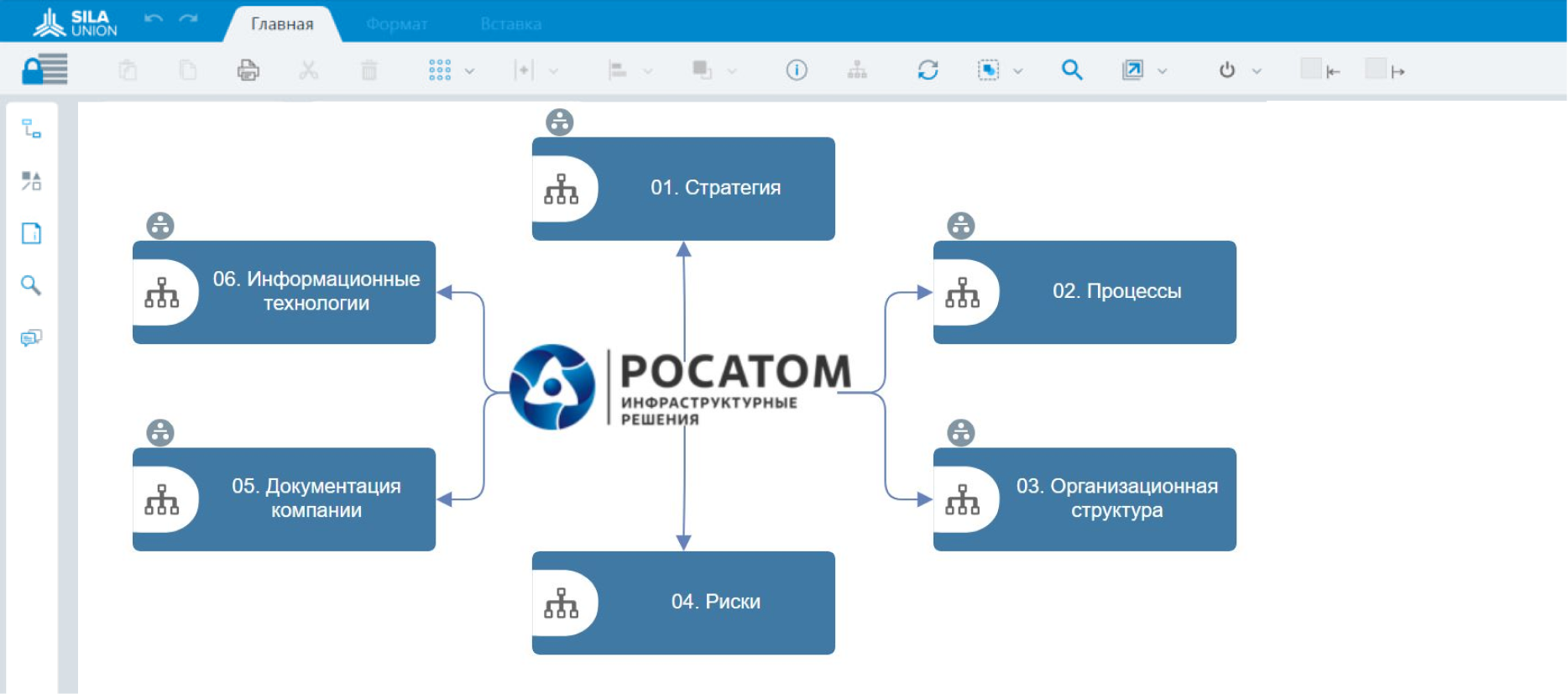
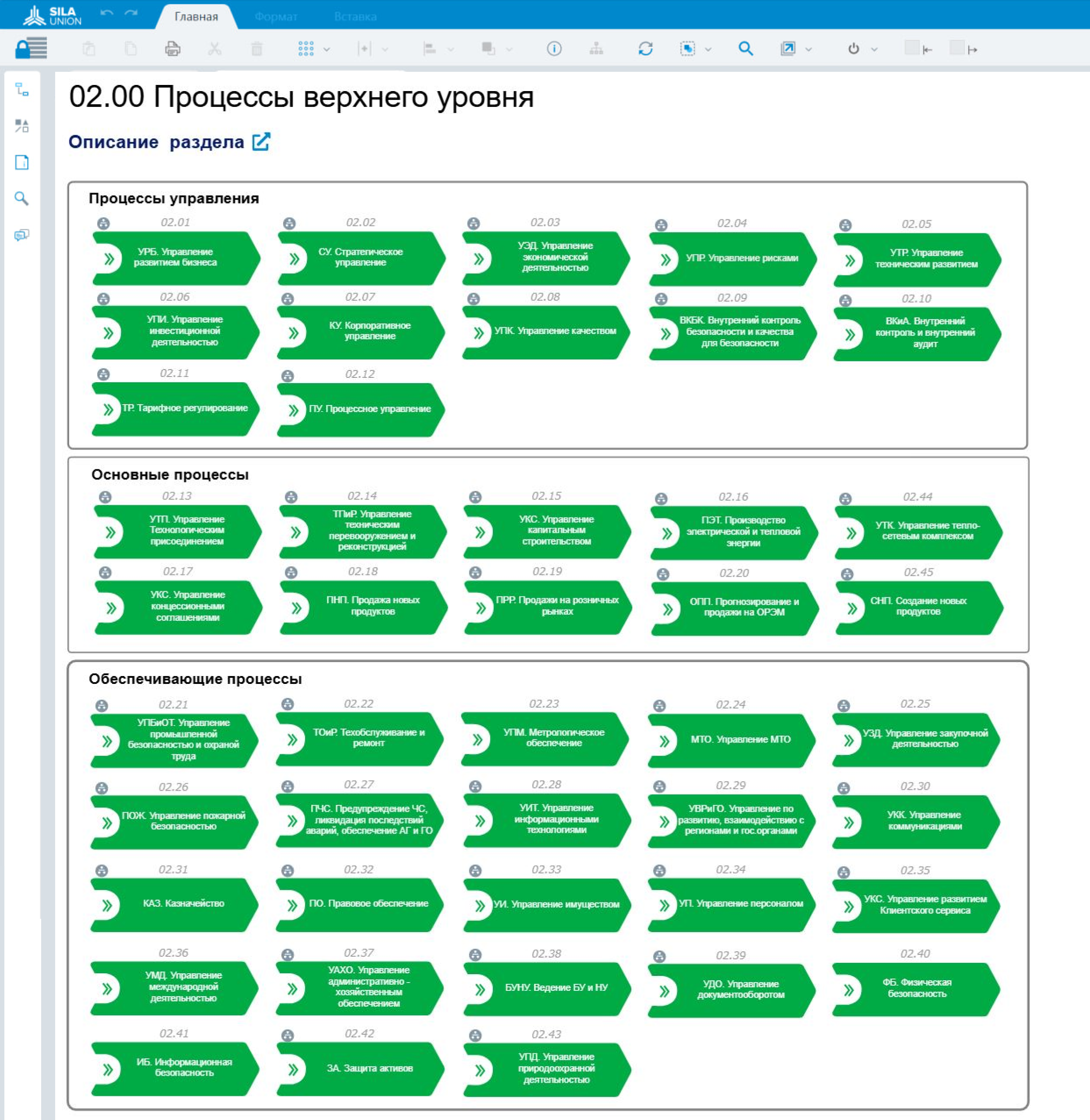
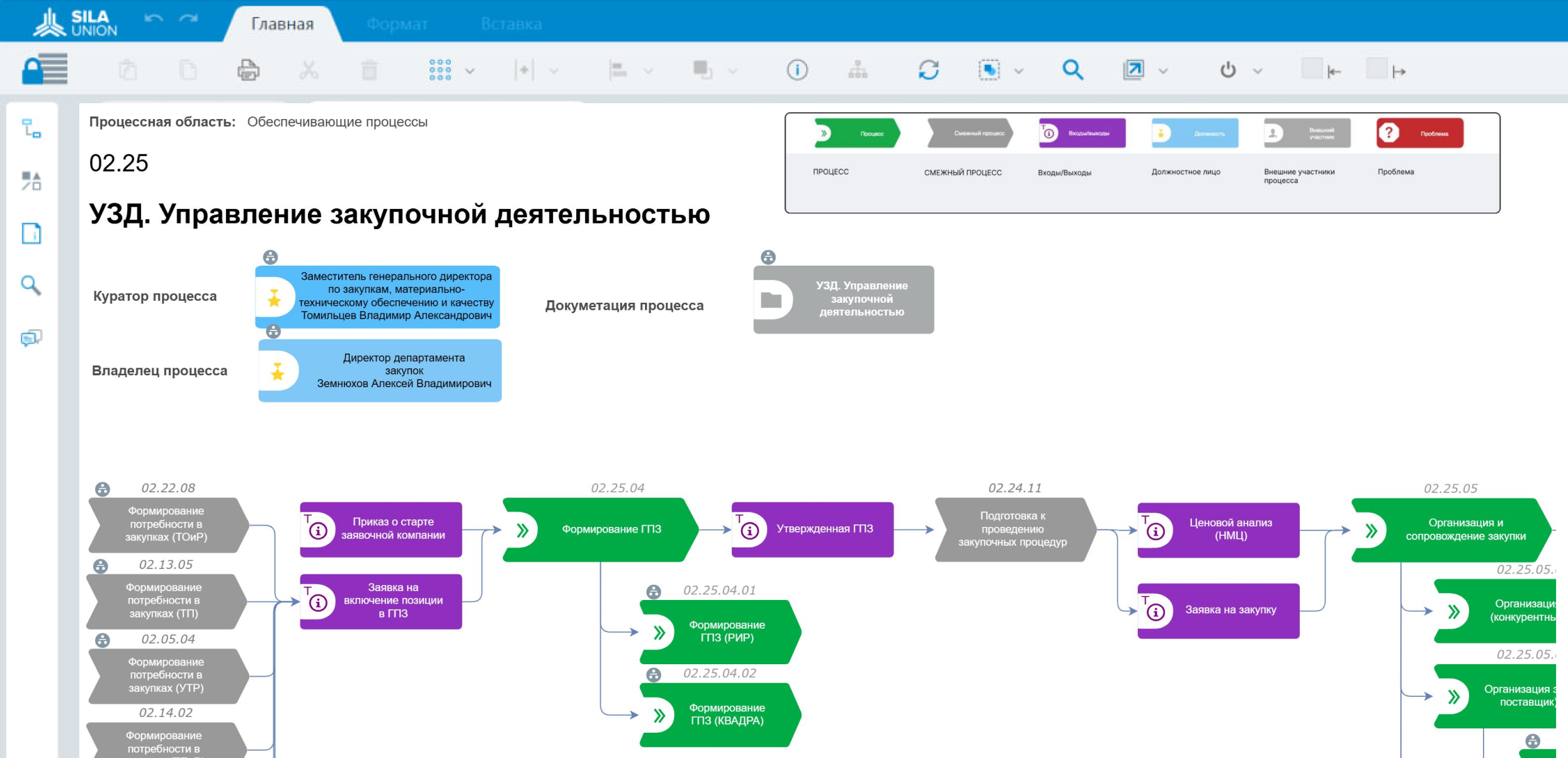
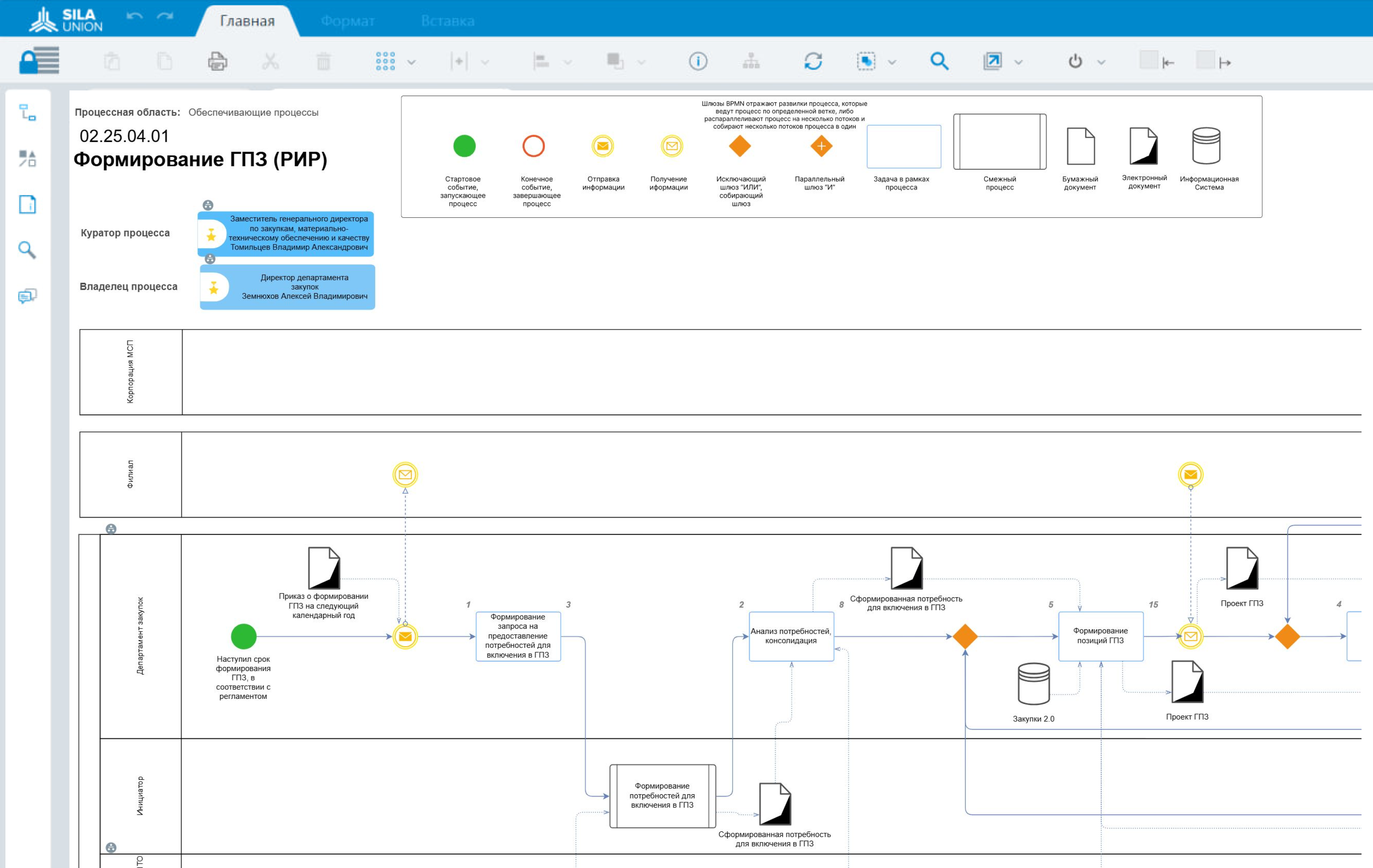
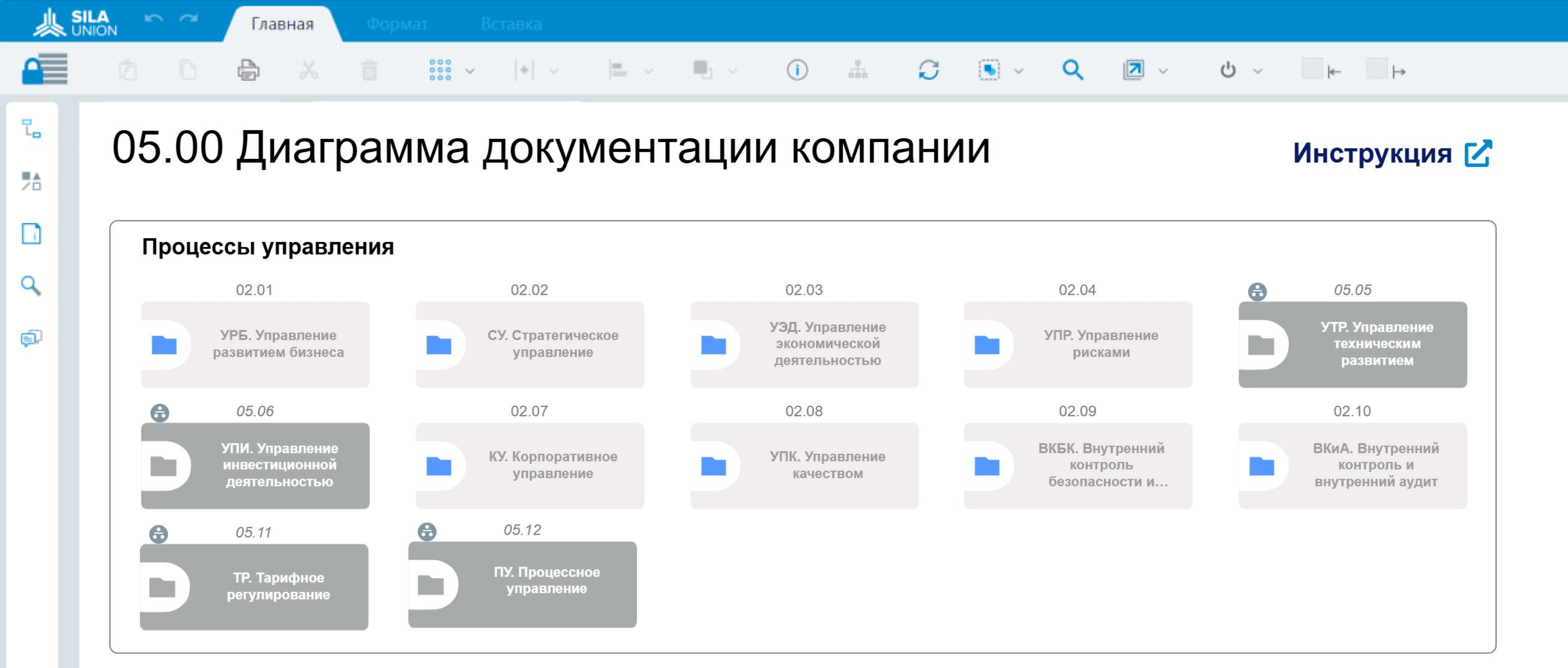
Employee Engagement and Training
Change management was one of the key project tools, with a dedicated plan that included activities such as business breakfasts, general educational lectures on functional areas, and other team-building events. A Telegram channel was created to communicate the integration process and explain key changes.
A Change Team was specifically formed and trained, consisting of motivated individuals willing to act as change ambassadors, demonstrating engagement in the integration process by personal example.
Challenges
The key challenges were tight deadlines and dynamically changing local requirements from internal stakeholders. This issue was addressed by quarterly plan reviews and updates.
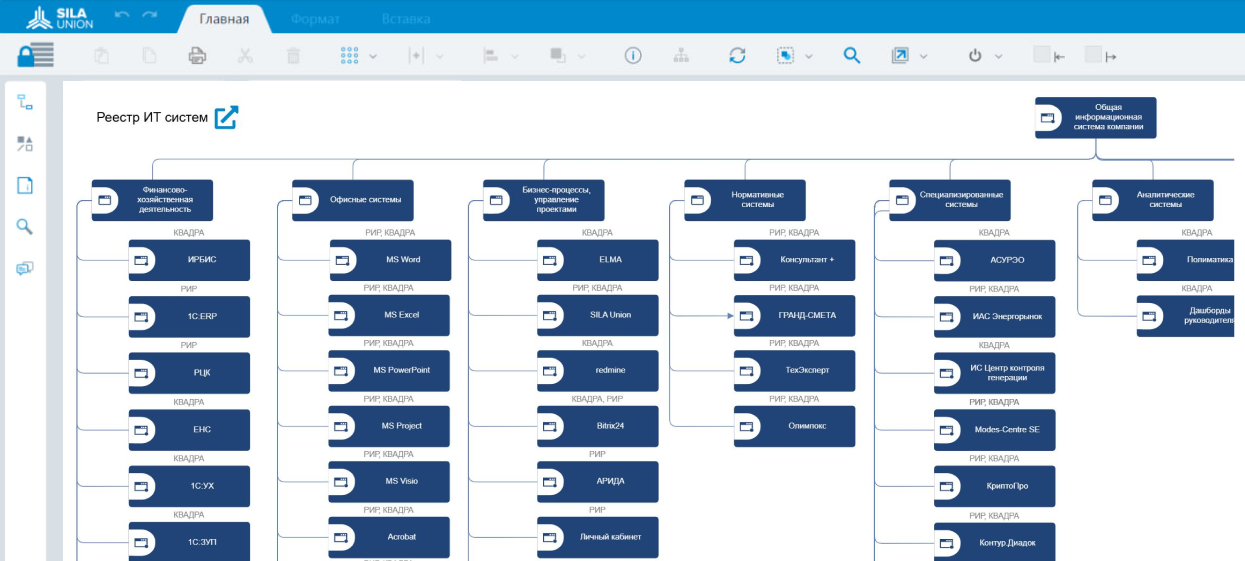
Project Results
Through this approach, the new process model was implemented, and organizational changes were carried out, optimizing the workforce of the Unified Management Company while exceeding all business performance indicators of the division.
By merging organizational structures, over 300 million rubles were saved, and through process optimization projects, an additional economic benefit of over 100 million rubles was achieved.
Future Plans
The next steps involve scaling the process model to regional branches and training an AI-powered process library to create a chatbot for employees, which will serve as a knowledge base for processes, procedures, organizational structures, documentation, and more.